Service and parts for plate heat exchangers
Heat exchangers are usually designed for a lifetime of 20 or 25 years. In fact, they are often in service for much longer. Plate heat exchangers with fully welded plate pack and Thermoplate heat exchangers are gasket free. Thus, avoiding the cost-intensive replacement of gaskets which is regularly required with Plate & Frame heat exchangers after a few years, because of the aging of elastomer materials, chemical attack, or thermal degradation, increasing life cycle costs. "Where no gaskets are, no leaks can occur."
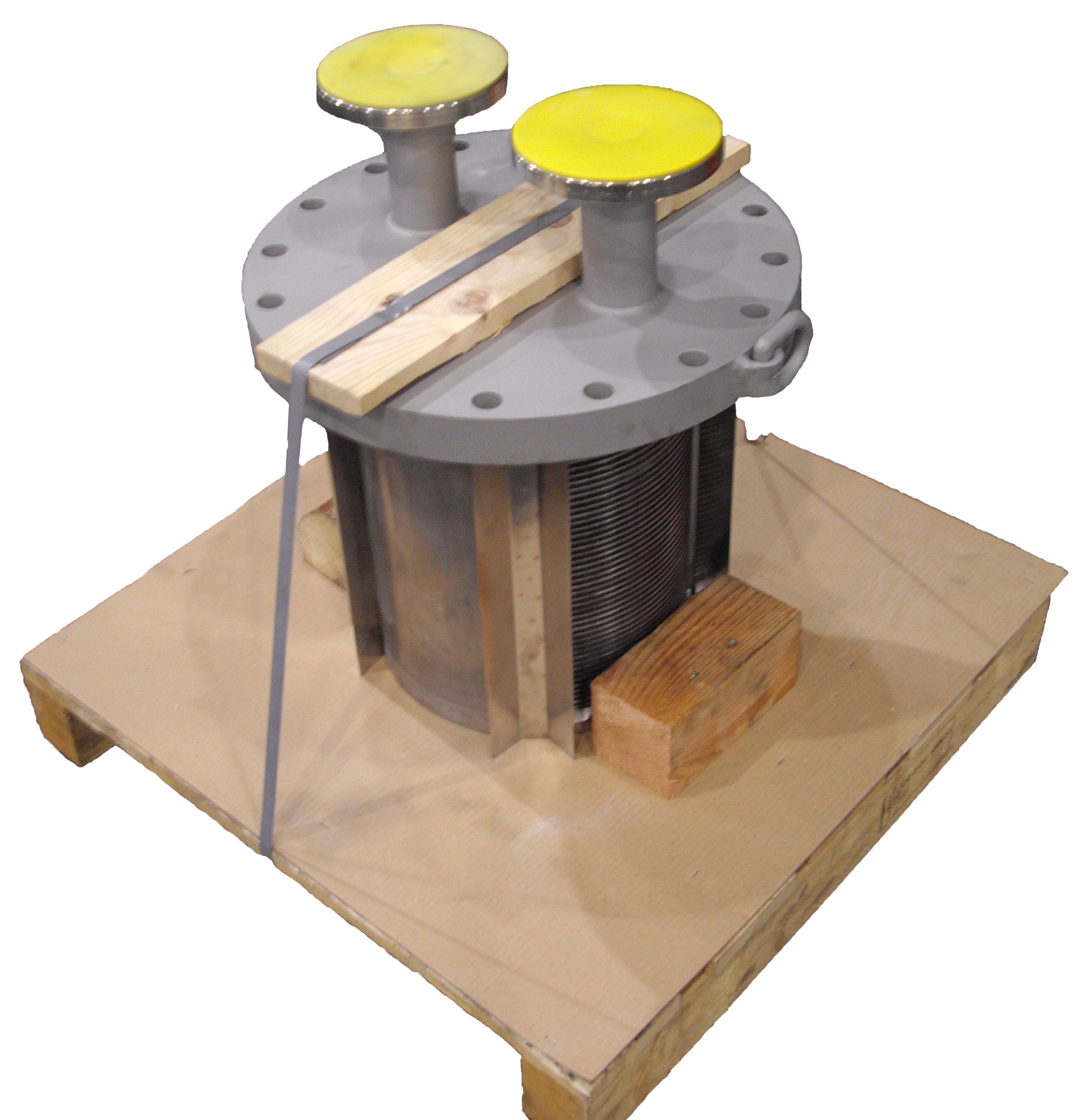
Replacement packs for openable heat exchangers
GESMEX supplies plate pack for easy replacement in openable Plate & Shell heat exchangers. Downtime can be minimised, and service work on the plate pack can be carried out in parallel with the ongoing production. Graphics: Plate pack for an XPS plate heat exchanger, ready for shipment
Experts on site
GESMEX has experienced engineers and field service technicians, when it comes to consultation and installation supervision, commissioning or during revamp work. We support with inspections and monitoring of existing plants, providing an optimized solution when debottlenecking, or upgrading.
Condition monitoring of heat exchangers
Operating data analysis
Operating parameters such as temperatures, flow rates and pressure losses should be observed over long periods of time to obtain the optimum service date, and for appropriate service recommendations. Performance calculations can be done on GSX-Calc to estimate the performance of GESMEX heat exchang-ers.
Videoscopy on heat exchangers
In videoscopy examinations the aim is to review and assess the heat transfer surfaces. Depending on the condition of the surfaces, suitable cleaning measures can be determined, or the success subsequently verified. The heat exchanger must be drained for videoscopic investigations and access via nozzles to the equipment inside must be possible. The examinations can take place in the plant or in an equipment workshop.
Infrared measurements
By infrared measurements on heat exchangers, the temperature distribution in the unit can be determined. With sufficiently large temperature differences it is possible to view the temperature profiles of the flowing hot and cold media. The measurements must be carried out during plant operation and under defined operating conditions. As a result, evaluation of the heat exchanger performance and any possible optimization can be identified.
Cleaning of heat exchangers
Cleaning of GESMEX - heat exchangers is usually carried out by the maintenance personnel of the plant, or by local service providers. This reduces the dependancy on shipping the unit, or personnel to site and expedites the cleaning. GESMEX, at customer´s disposal, supports and advises on cleaning agents and for optimum cleaning methods.
When cleaning of heat exchanger plates, fouling layers areremoved from the heat transfer surface, i.e. deposits formed during operation, which hinder the heat transfer. During operation any combination of the following kinds of fouling are possible:
-
crystallisation fouling
-
particle fouling (also sedimentating fouling)
-
corrosion fouling
-
biological fouling
for welded plate heat exchangers basically two cleaning methods can be used:
-
mechanical cleaning
-
chemical cleaning
Mechanical cleaning
Depending on the design and installation of the Plate & Shell heat exchanger, mechanical cleaning methods can be differentiated as:
- back flushing
- high-pressure cleaning (for openable units only)
Back flushing causes the whirling up of loose deposits, which are then carried with the media stream out of the heat exchanger. Prerequisite for this method is that the piping system is configured to enable a reversal in flow. The high-pressure cleaning is only applicable to openable units. Tthe disassembled plate pack are cleaned by steam or high pressure water jet (800 to 1000 bar). When cleaning with water, the water should be preheated to between 50 and 60 °C. The cleaning media is jetted into the flow channels directly. Jet blasting the open face of a plate is generally not possible welded plate packs. On the opposite side, free drainage of the cleaning medium must be possible. After cleaning, the cleaning medium shall be disposed environment-friendly.
Chemical cleaning
Depending on the design of the Plate and Shell heat exchanger, chemical cleaning can be differentiated in:
- CIP cleaning (Cleaning In Place), for openable and fully welded units
- immersion bath cleaning (for openable units only)
CIP cleaning requires a fixed installation or mobile CIP cleaning system. Isolation valves are required, and suitable connections for feeding and returning the CIP fluid are needed. The first step is to flush with warm water, recirculate and drain. After that for several hours a cleaning solution is pumped against the flow direction of normal operation. Finally it is recommended to flush through with warm water to rinse any chemicals out. GESMEX recommends using industrial cleaning chemicals from specialised manufacturers that are tailored to remove certain deposits and are specifically developed for this. To prevent damage to parts in contact with the CIP fluid, acids and bases must not be used in concentrated, form but only in solutions:
- citric acid 7%
- nitric acid 2%
- phosphoric acid 5%
- sulphuric acid 5%
- caustic soda 5%.
The immersion bath cleaning is only applicable to plate packages in openable Plate & Shell heat exchangers. Here the disassembled plate pack is immersed in a warm bath with cleaning chemicals for several hours. The cleaning chemicals manufacturers instructions must be followed for preparation and disposal. To avoid damage to parts of the plate pack the same concentration limits as for CIP cleaning apply. The cleaning medium shall be disposed environment-friendly after use.