Function of Thermoplate Heat Exchangers
The pillow-shaped design of the Thermoplates permits optimum flow with sufficient turbulence, creating excellent conditions for efficient heat exchange while minimising pressure loss.
XPT - Thermo Plate heat exchangers consist of an arrangement of two metal plates that are completely welded together along the sides. These plates are also connected by spot welds distributed across the entire heat transfer area. The position, number and pattern of the spot welds determine the operating pressure and the flow pattern. During the manufacturing process, the welded plates are pressed apart using water or gas until they reach the desired channel cross-sections. The resulting hollow space for the medium is referred to as the “lamellar side”. The channel cross-section influences both the heat transfer and the pressure loss.
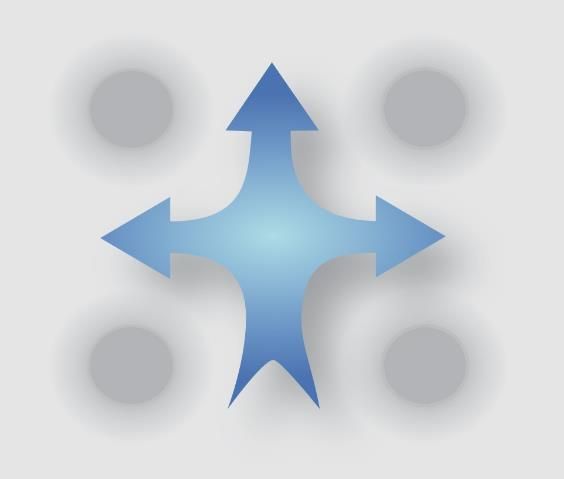
Spot weld pattern
Flexible distance between Thermoplates
The spacing between the welded pairs of Thermoplates is variable, depending on the medium used between the plates. For certain applications additional weld seams are included, to optimize the flow distribution. The inclusion of such flow channels also changes the flow velocities and the heat transfer coefficients.
Thermo Plates in rounded shape
Multipass design at lamelarside
The pillow-shaped design causes turbulence and creates a self-supporting structure. No forces are transferred outward from the individual Thermoplates to the next plate– these forces would otherwise need to be absorbed by the casing.
In principle, XPT - Thermoplates can be manufactured in any size and in a variety of shapes and are thus easy to fit into or onto existing tanks, columns, etc. XPT heat exchangers are also suitable for applications involving contaminated gases or liquids. The smooth, undulating surface allows for CIP cleaning or high-pressure cleaning with good results in comparison to other types of heat exchanger.
For certain applications the heat exchangers can be fitted with permanently installed CIP systems.
Fully welded Thermo Plate heat exchangers are individually optimized for each project in accordance with the technical and commercial specifications, e.g. for heating and cooling, for use as condensers or as falling film evaporators.